The adventure with inspection robots has started for some of us in 2015 when together with colleagues from Poznań University of Technology we have had a meeting in KGHM HQ. A research group in KGHM Cuprum led at that time by Rado Zimroz joined the consortium (ETH Zurich, University of Edinborough, Poznań University of Technology, University of Pisa, University of Oxford, QBROBOTICS SRL and ANYBOTICS AG) to conduct a research project entitled The subTerranean Haptic INvestiGator, or THING for short! Official website here.
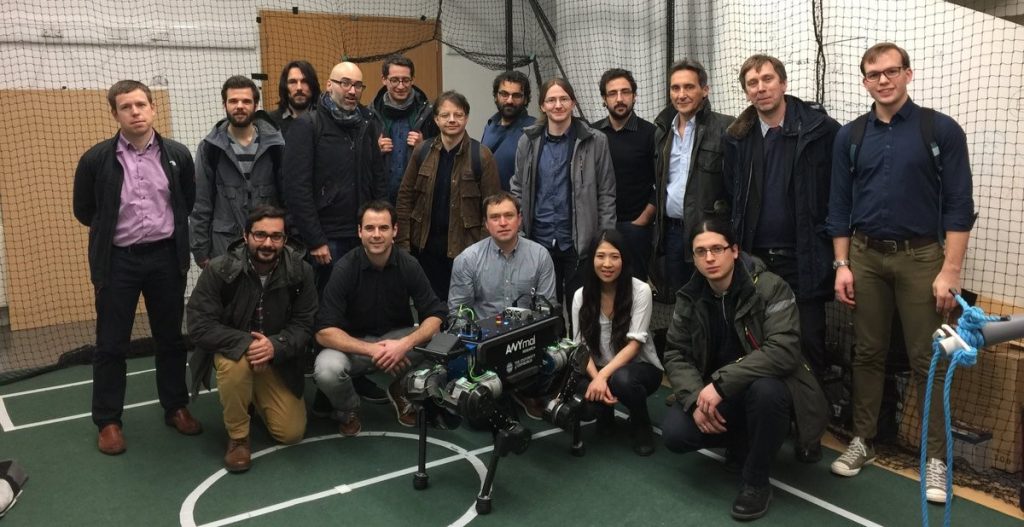
Why exactly do we need inspection-oriented robotic solutions in the mining industry?
As we wrote in our paper:
Deep underground mines impose new challenges for the mining industry when searching for new hardly accessible deposits. These challenges are related to locations of deposits, their geometry, and harsh environment (dust, temperature, and humidity) including natural hazards (gas emission, water, and seismic events). Even nowadays, miners are allowed to work during shorter (6 h only) shifts. It is expected that this period will be shortened in the following years. More demanding conditions in the mine focus activities of companies and research institutions toward introducing robots to the mines. There are many successful examples of autonomous machines operated in the mine, robotized processes, and application of UAVs in open-cast mines. Unfortunately, applications of robotics in an underground mine are still limited. In this paper, we will introduce recently launched project THING, supported by the H2020 EU programme that is devoted to the usage of autonomous quadrupedal robot ANYmal for inspection of infrastructure in a deep copper ore mine. To be more precise, we will discuss how to support daily maintenance procedures for belt conveyors. In the paper, we will briefly present ANYmal, highlight main research tasks from maintenance and robotic perspective and discuss possible inspection missions for belt conveyor maintenance.
Why should inspection robots be used in deep underground mines? Proceedings Article In: pp. 497–507, Springer International Publishing, 2019. |
Unfortunately, at the beginning of 2019, we have left KGHM Cuprum and consortium, but we still love inspection robots. We have acquired mobile platforms to use them for maintenance purposes.

Instead of traditional, visual, thermal, noise inspection performed by maintenance staff…
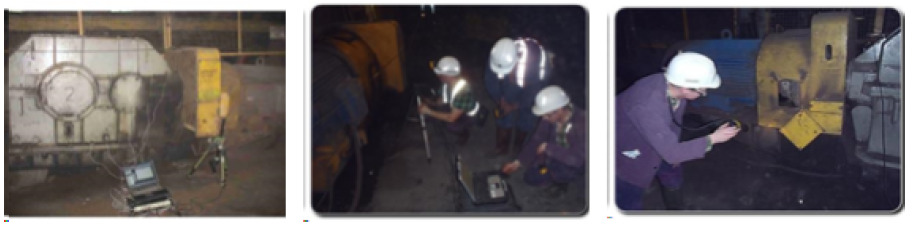
…we would like to use robots equipped with a visual spectrum camera, IR camera, microphone, or various other sensing equipment. Our collaboration with the Mechanical Engineering Faculty at WUST is very promising (special thanks to Jarek Szrek!).
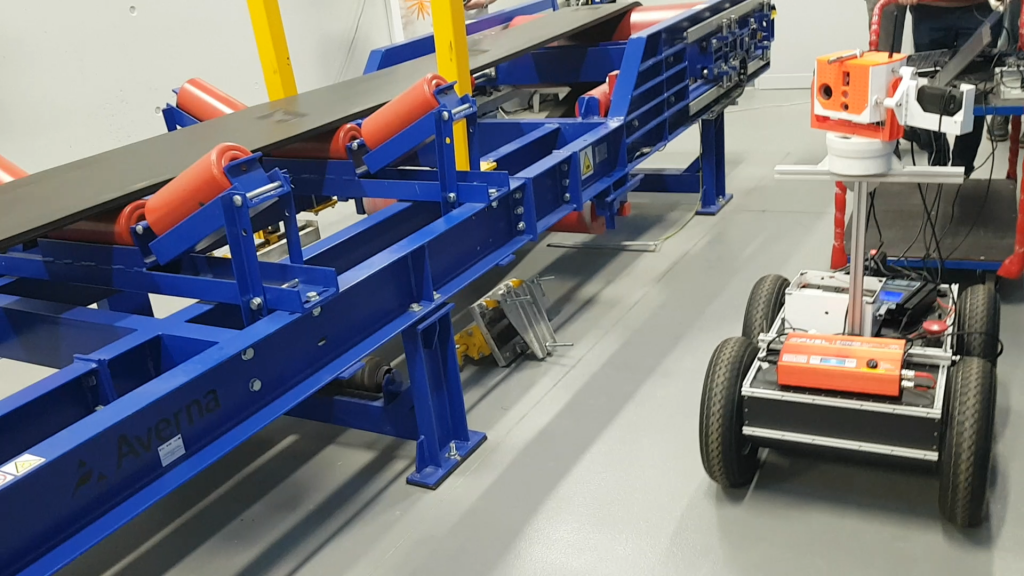
Since 2020 we are happy to be part of AMICOS. Together with many respectable partners from all over Europe, we developed the considered solution over 3 years. See Menu “Projects” for more.
As we have been developing the solutions for the project, several interesting technical approaches have been used. We have prepared three sets of training materials so that you can learn useful information about them.